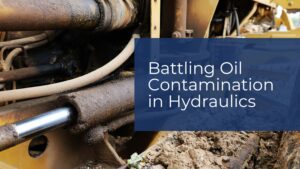
Hydraulic systems are critical to manufacturing operations but face wear and tear from high-pressure, high-demand environments. Allied Hydraulic offers expert repair, rebuild, and replacement services for pumps, motors, cylinders, and valves. With precision repairs and dynamic pressure testing, we keep your equipment running smoothly and efficiently.
Hydraulic systems are critical to manufacturing operations but face wear and tear from high-pressure, high-demand environments. Allied Hydraulic offers expert repair, rebuild, and replacement services for pumps, motors, cylinders, and valves. With precision repairs and dynamic pressure testing, we keep your equipment running smoothly and efficiently.
Hydraulic system issues can lead to costly downtime and disrupt productivity. In this guide, we cover essential troubleshooting steps for common hydraulic failures like low pressure, overheating, leaks, and unusual noises. Learn how to diagnose and resolve these problems effectively and discover preventive maintenance tips to keep your hydraulic equipment running at peak performance.
Hydraulic cylinders are essential to many industrial systems, but over time, issues like seal leaks, bent rods, and surface damage can occur, leading to costly downtime. In this blog, we explore the most common hydraulic cylinder failures, how to diagnose these issues through visual inspections and performance testing, and provide step-by-step repair tips, such as replacing seals and rods or resurfacing damaged components. Additionally, we offer preventative maintenance advice to help extend the life of your hydraulic cylinders and avoid future problems.
When it comes to hydraulic system repairs, one critical choice that operators face is deciding between Original Equipment Manufacturer (OEM) parts and aftermarket parts. Both options come with distinct advantages and trade-offs, but understanding these differences is crucial for maintaining the efficiency, longevity, and safety of your hydraulic machinery.
By focusing on crucial areas like keeping hydraulic fluid clean, inspecting hoses for wear, and monitoring system pressure, you can catch potential issues early and ensure your machinery operates efficiently.
Hydraulic component repair is crucial in the construction industry, as it ensures the reliability and efficiency of heavy machinery, minimizes downtime, and reduces the risk of costly breakdowns, ultimately enhancing overall project productivity.
Oil contamination in hydraulic systems can lead to early pump failure and reduced efficiency. Regular maintenance, such as oil analysis and filter replacement, is crucial to prevent costly damage.