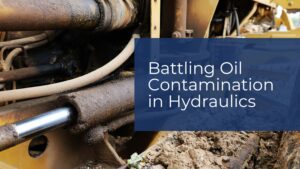
We’re looking forward to working with you. Whether you have questions about products or services, our team is ready to help.
Hydraulic systems are the driving force behind heavy-duty machinery in industries ranging from construction to manufacturing. However, these systems are highly susceptible to a hidden danger: oil contamination. This often-overlooked issue can lead to early pump failure, reduced system efficiency, and costly downtime.
What Is Oil Contamination?
Oil contamination occurs when foreign particles, water, air, or other substances infiltrate hydraulic fluid. These contaminants can enter the system through external sources or internal wear, and if left unchecked, they can cause significant damage to hydraulic components like pumps and cylinders.
Impact on Hydraulic Systems
Contaminants in hydraulic oil act as abrasive agents, causing wear on internal parts, reducing lubrication, and increasing friction. This leads to premature failure of hydraulic pumps and a decline in overall system performance. Water contamination, in particular, is a major concern, as it can lead to rust, oxidation, and loss of hydraulic fluid’s essential properties, resulting in system inefficiency and responsiveness issues.
Identifying Oil Contamination
Operators can spot oil contamination through simple visual checks:
Prevention and Maintenance
Preventing oil contamination requires a proactive approach:
By understanding the risks of oil contamination and implementing preventive measures, operators can maintain the efficiency and longevity of their hydraulic systems, avoiding the costly consequences of neglect.
Hydraulic systems are the driving force behind heavy-duty machinery in industries ranging from construction to manufacturing. However, these systems are highly susceptible to a hidden danger: oil contamination. This often-overlooked issue can lead to early pump failure, reduced system efficiency, and costly downtime.
What Is Oil Contamination?
Oil contamination occurs when foreign particles, water, air, or other substances infiltrate hydraulic fluid. These contaminants can enter the system through external sources or internal wear, and if left unchecked, they can cause significant damage to hydraulic components like pumps and cylinders.
Impact on Hydraulic Systems
Contaminants in hydraulic oil act as abrasive agents, causing wear on internal parts, reducing lubrication, and increasing friction. This leads to premature failure of hydraulic pumps and a decline in overall system performance. Water contamination, in particular, is a major concern, as it can lead to rust, oxidation, and loss of hydraulic fluid’s essential properties, resulting in system inefficiency and responsiveness issues.
Identifying Oil Contamination
Operators can spot oil contamination through simple visual checks:
Prevention and Maintenance
Preventing oil contamination requires a proactive approach:
By understanding the risks of oil contamination and implementing preventive measures, operators can maintain the efficiency and longevity of their hydraulic systems, avoiding the costly consequences of neglect.
We’re looking forward to working with you. Whether you have questions about products or services, our team is ready to help.