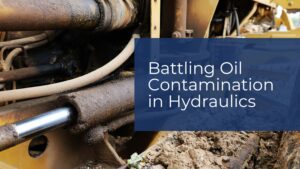
We’re looking forward to working with you. Whether you have questions about products or services, our team is ready to help.
When you’re working around pressurized oil, a simple misstep can turn a routine service call into a five-figure fine, or worse, a life-altering injury. That’s why every maintenance crew needs a hydraulic lock-out/tag-out (LOTO) checklist that meets OSHA’s 29 CFR 1910.147 requirements. This guide walks you through the exact seven-step process, the tools you’ll need, and the costly mistakes inspectors keep writing up, so you can keep people safe and avoid downtime-draining penalties.
Residual line pressure & accumulators
Even a few hundred psi can eject oil or components with lethal force.
Gravity-loaded actuators
Elevated booms or presses may drop when pressure bleeds off.
Thermal expansion
Oil heats up after shutdown and spikes pressure in “dead-head” lines.
Multiple energy paths
Pumps, accumulators, nitrogen backs, and gravity all require separate isolation points.
Residual pressure (lines, accumulators, cylinder chambers)
Even a few hundred psi can eject hot oil or parts with lethal force.
Gravity-loaded actuators
Elevated booms, presses, or buckets can drop suddenly when pressure bleeds off.
Thermal expansion
Oil that heats up after shutdown spikes pressure inside any “dead-head” line.
Multiple energy paths
Pumps, accumulators, nitrogen backs, and gravity each require separate isolation.
1. Prepare & notify
Identify every hydraulic energy source; alert affected employees.
Trace the schematic – don’t rely on memory.
2. Safe shutdown
Stop the machine in a controlled manner; cycle functions to release working pressure.
Use inch/jog controls where available.
3. Isolate all energy
Close pump isolation valves, vent accumulators, disconnect quick couplers as needed.
Tag every valve position.
4. Dissipate stored energy
Bleed down to 0 psi on both sides of cylinders via relief valves or test points.
Keep gauges attached until zero. |
5. Apply locks & tags
Affix personal locks and durable tags that meet ANSI Z535.5 design rules
Use group lock boxes on multi-tech jobs.
6. Verify zero energy
Try to cycle controls and read gauges; §1910.147(d)(6) requires active verification
Use group lock boxes on multi-tech jobs.
7. Return to Service
Remove tools, reinstall guards, notify staff, and clear locks/tags in reverse order.
Only the person who applied a lock may remove it.
Need a field-ready version? Download the one-page PDF checklist.
When every minute of uptime counts, a solid lock-out/tag-out routine isn’t just “safety paperwork”, it’s cheap insurance against catastrophic downtime and six-figure fines. By following the seven steps above and stocking the right bleed-down tools, you’ll keep your crew protected and your hydraulics ready for the next shift.